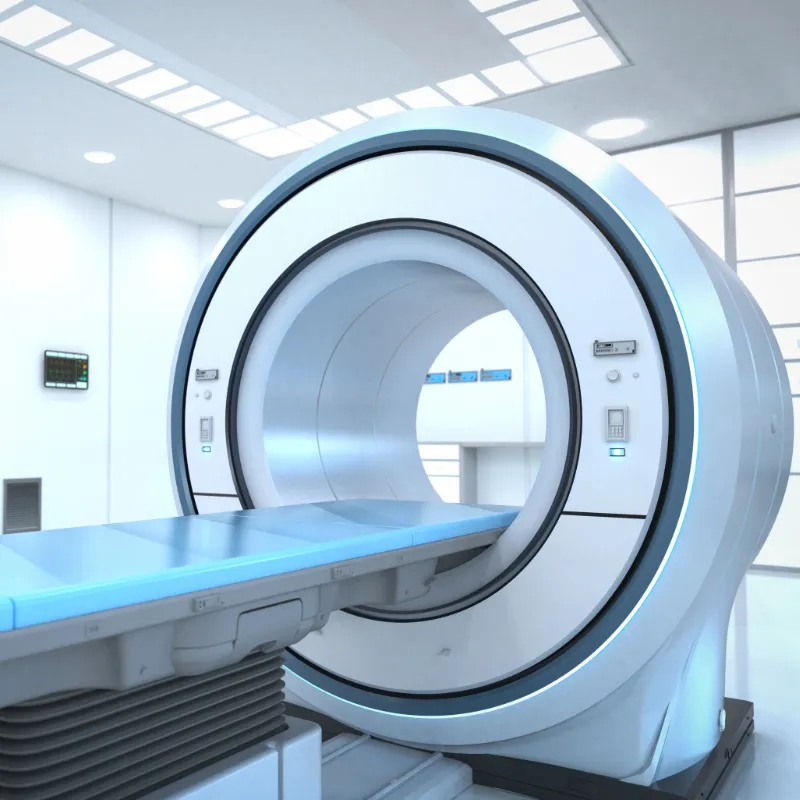
Medical Electronics Manufacturing
At FermionX, we offer full medical electronics manufacturing support to medical device and laboratory customers.
Our team has a deep understanding of the regulatory processes, controls and audit requirements within the medical industry.
With our ISO 13485 certification and strict quality controls, we guarantee uncompromising quality, traceability, and safety in every product. Our medical device customers can rest assured that their devices are reliable and effective, even in the most critical environments.
We also manufacture our own brand laboratory equipment. Seward Stomacher® products are used globally, across a wide range of microbiology testing and production.
Switch your medical device manufacturing to a UK supplier with dedicated, experienced staff and a proven track record for quality.
Medical Electronics Manufacturing Services
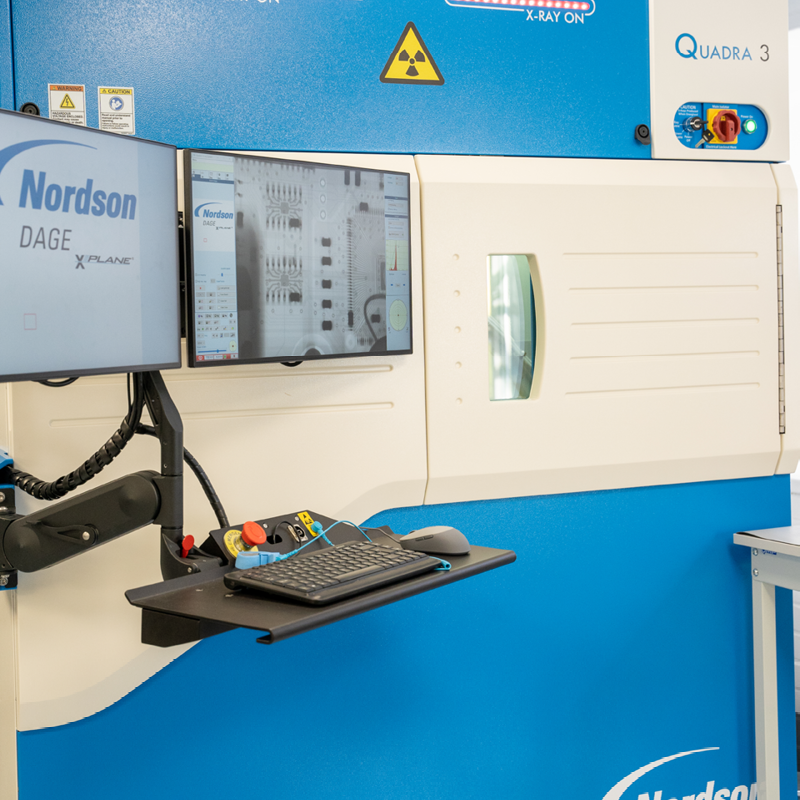
AOI and X-Ray Inspection
Our boards are inspected by using a Mantis or ASH Inspex HD 1080p camera system, in addition to an FX 940 In-Line Automated Optical Inspection. For medical device PCBs that can’t be inspected visually, we have a Nordson DAGE Quadra 3 X-ray inspection system.
Obsolescence management
We offer sourcing support for obsolete components for the medical market through our extensive supply network, and product phasing support for cost controls on last time buys.
Working closely with our supply chain partners through our ISO policies, audits and performance data means we can be certain that our supply is trustworthy and dependable.
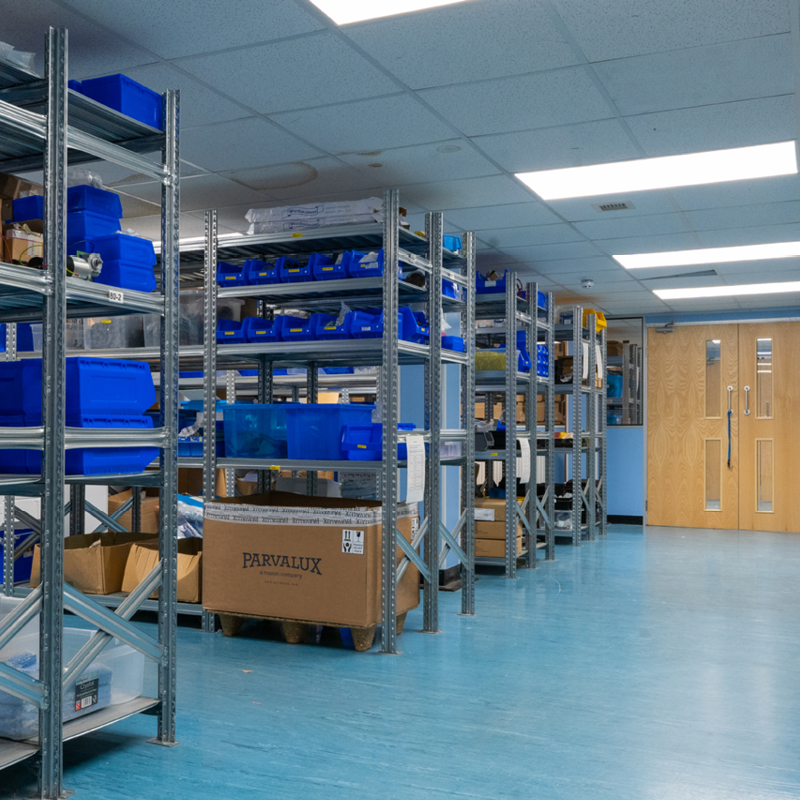
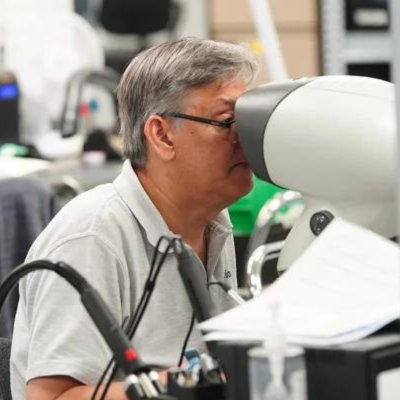
Quality Control
The medical device industry has a high degree of regulatory oversight, therefore reliability and attention to detail are paramount. FermionX is committed to maintaining the highest standards of system and process controls and ensuring we meet all regulatory requirements.
Our ISO 13485 certification assures our medical device customers of the highest quality standards. We also hold 9001 and COSHH certification, and operate to the requirements of ISO 14001 for environmental management systems.
FAQs
What is the purpose of ISO 13485 certification?
ISO 13485 is a certification standard that sets out the requirements for a comprehensive quality management system for medical devices. The purpose of ISO 13485 certification is to ensure that medical devices are manufactured to meet the highest levels of quality, traceability, and safety.
What are the benefits of partnering with an ISO 13485 certified CEM?
By partnering with an ISO 13485 certified CEM, you can rest assured that your medical devices will be manufactured in accordance with the standard’s rigorous requirements. This means that your devices are guaranteed to be reliable and effective in critical environments, giving you and your customers peace of mind.
We understand that intricate medical devices demand for specialised engineering expertise to ensure success in critical environments. With ISO 13485, we have the necessary knowledge and experience to handle every aspect of the manufacturing process. Saving you valuable time and resources, and allowing you to focus on your core competencies whilst helping you to get your products to market faster.
What internal changes have you made to secure this certification?
Our tireless efforts to improve internal processes and implement effective software systems have played a crucial role in securing this standard.
We’ve implemented stringent EPA control protocols, access control testing and increased ESD protection equipment for all production staff. Our premises are also climate controlled in order to minimise the risk of damage to sensitive components in medical devices.
We’ve recently implemented an ERP/MRP system upgrade across the business that traces our production process from initial quote through to shipping, allowing us to mitigate any risks to production and identify errors that could occur.
We can also offer customers a complete overview of their production status, from start to finish.
Request a quote
Speak to our expert team today to find out how we can support you on your next project.
Read our quote requirements here
Case studies and testimonials
Manufacturer of blood monitoring and fluid management equipment
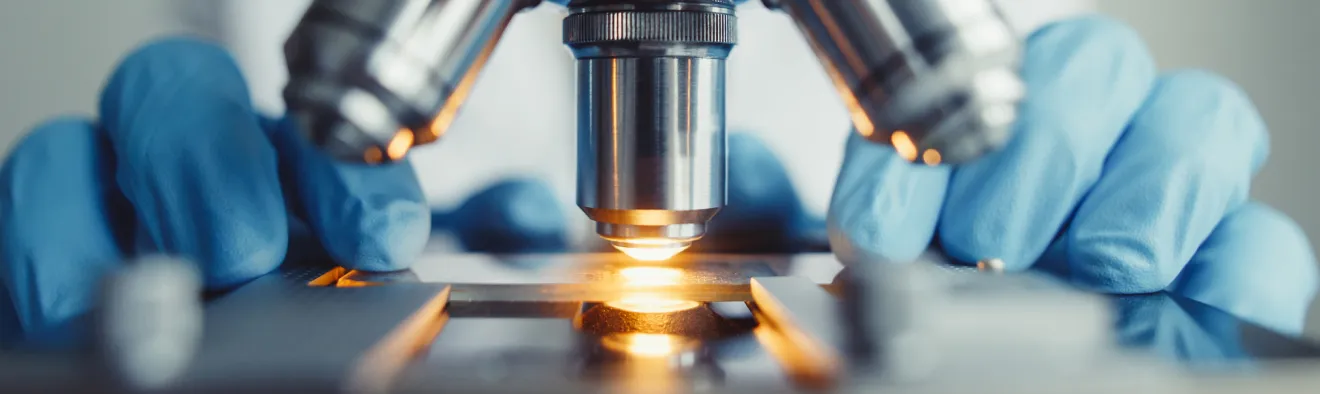
After working with non-communicative suppliers in the past, the company needed a supplier who could deliver consistently, and a direct line of contract with their operations team on the ground. The FermionX operations team communicate directly with their counterparts, meeting frequently and keeping them in the picture.
FermionX have developed a very stable and trusting working relationship, whilst the company continues to bring new projects to their manufacturing partners.
“We can confidently go to FermionX to talk about our needs. They communicate well with our team, so that we always know exactly where we are with our supply.” Supply Chain Manager